Selecting the appropriate foam composite is a critical part of ensuring the success of your projects, especially in industries requiring lightweight yet durable materials such as UAV (unmanned aerial vehicle) manufacturing and aerospace applications. Foam composites, like Rifeng F foam core composite, are engineered to offer superior strength, impact resistance, and weight efficiency. By understanding design considerations, comparing different foam types, and assessing factors like density and structural integrity, you can make the best choice for your project. Here's a guide to help you make an informed decision.
Table of contents:
Design Considerations for Foam Core Selection
Comparing PMI, PVC, and PET Composites for UAV Usability
Factors Influencing Density and Structural Integrity
Custom Solutions From Leading Foam Composite Suppliers
Design Considerations for Foam Core Selection
When choosing foam composites for your project, it's essential to consider the specific design requirements of your application. For UAVs, lightweight materials are paramount as they directly impact flight efficiency and fuel consumption. Here, foam composites like Rifeng F stand out due to their fine cell structure, which keeps resin uptake minimal, adding no excess weight. Additionally, specific design attributes such as environmental resistance, heat tolerance, and ease of machining affect the selection process. Rifeng F, for example, offers excellent heat distortion resistance (up to 200°C) and is easily thermoformed or CNC-machined, making it ideal for complex geometries and precise component requirements.
Comparing PMI, PVC, and PET Composites for UAV Usability
Not all foam core composite are created equal. Three commonly used types are PMI (Polymethacrylimide), PVC (Polyvinyl Chloride), and PET (Polyethylene Terephthalate), each with unique attributes. PMI foams, like Rifeng F, excel in UAV and aerospace industries because of their high strength-to-weight ratio and exceptional dielectric properties, which make them ideal for antennas and radome structures. PVC foams are cost-effective and offer good durability but may not provide the same lightweight advantage as PMI. PET foams are often selected for their sustainability and recyclability but are typically less robust than PMI. For high-performance applications like UAV construction, PMI foams are often the go-to due to their superior mechanical properties and compatibility with metallic facing materials.
Factors Influencing Density and Structural Integrity
Density and structural integrity are key factors in determining the performance of foam composites in specific applications. Foam composites with customizable densities, like Rifeng F, allow engineers to balance strength and weight precisely. For example, Rifeng F offers densities ranging from 32 kg/m³ for ultra-lightweight needs to 110 kg/m³ for heavier-duty applications requiring higher strength. Structural integrity is also impacted by tensile strength, compressive strength, and shear properties. Rifeng F provides impressive mechanical properties, such as a compressive strength of 2.25 MPa at its highest density and high elongation at break, ensuring durability under demanding loads. By analyzing your project requirements against density and structural benchmarks, you can select a foam composite that enhances both performance and reliability.
Custom Solutions From Leading Foam Composite Suppliers
When it comes to foam composites, collaboration with a trusted supplier opens doors to customized solutions tailored to your project’s unique demands. Rifeng F foam core materials, for instance, are available in various dimensions, thicknesses, and tolerances to fit diverse use cases. Their closed-cell structure prevents unnecessary resin absorption during composite construction, optimizing weight savings and structural efficiency. Leading suppliers also provide advanced processing capabilities, such as hand lay-up, vacuum infusion, and prepreg techniques, catering to the complex needs of high-performance industries. When seeking foam composites, choosing suppliers with extensive expertise and product versatility, like Rifeng, ensures you're equipped with the ideal material for your project.
Choosing the right foam composite is about aligning the material's attributes with your project’s objectives. With options like Rifeng F foam core composite offering high strength, low weight, and customizable properties, UAV manufacturers and aerospace professionals have reliable solutions at their disposal. Remember to assess the design, compare materials like PMI, PVC, and PET, and consider density and structural integrity factors for optimal results. By partnering with suppliers offering tailored solutions, you can elevate your project to new heights.
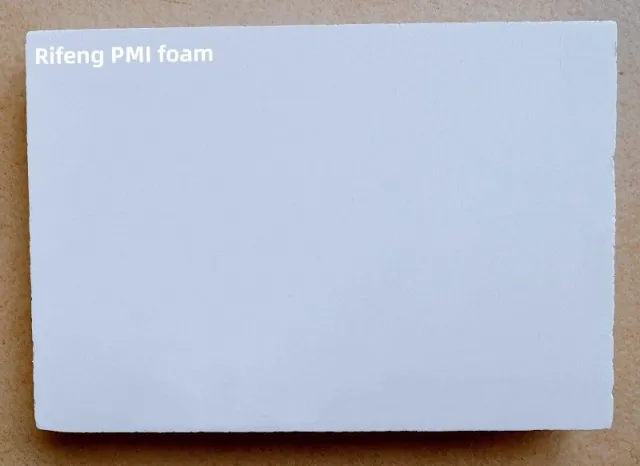
No comments:
Post a Comment