When it comes to manufacturing and assembly, even the smallest components play a significant role in the overall durability and performance of the final product. Among these components, fasteners are often overlooked, yet they serve as the backbone in holding everything together. Custom fasteners, in particular, offer unparalleled advantages over standard options, especially in specialized applications. By addressing unique project requirements, custom fasteners improve strength, safety, and the operational lifespan of products across a variety of industries.
Table of contents:
Why Custom Fasteners Offer Better Durability Than Standard Fasteners
How Customized Non-Standard Fasteners Enhance Product Safety and Performance
The Role of Custom Non-Standard Fasteners in Preventing Mechanical Failures
This article will explore how customized solutions can optimize durability and performance, discussing why they should be a staple for manufacturers intent on producing high-quality products.
Why Custom Fasteners Offer Better Durability Than Standard Fasteners
Custom fasteners are tailored to the specific needs of a product, making them inherently more durable than generic standard fasteners. Tailored engineering ensures that these fasteners are manufactured using materials and designs that suit the stress levels and environmental conditions the product will face. For instance, Vodafast's customized non-standard male-female fasteners are constructed from premium materials like carbon steel, alloy steel, and stainless steel. Each material is chosen based on the performance demands, ensuring long-lasting functionality even under extreme conditions. Furthermore, custom fasteners go through an array of finish options such as zinc plating, nickel plating, and hot-dip galvanizing. These coatings not only improve durability but also provide protection against corrosion and wear and tear, making them ideal for heavy-use industries like automotive, construction, and machinery. By removing the risk of incompatibility or poor material quality often found in mass-produced standard fasteners, custom solutions ensure maximum durability for the most demanding applications.
How Customized Non-Standard Fasteners Enhance Product Safety and Performance
While durability is critical, safety and overall product performance crucially benefit as well. Customized non-standard fasteners are specifically designed to match engineering drawings or samples, which means they seamlessly integrate with the product during assembly. This precision minimizes the risks of mechanical failures caused by loose parts, misalignments, or faulty connections. Vodafast’s manufacturing approach emphasizes exact specifications to boost not only the product's structural stability but also its operational safety. For example, industries requiring high-stress tolerance—such as those dealing with machinery or automotive applications—depend on fasteners that can withstand complex forces without compromising stability. The tailored design of customized fasteners ensures load distribution is optimized, thus avoiding weak points that could lead to part failure. The precision of non-standard fasteners also reduces manufacturing errors, which translates into better product performance, reduced maintenance costs, and higher user satisfaction in the long term.
The Role of Custom Non-Standard Fasteners in Preventing Mechanical Failures
Manufacturing defects can compromise the structural integrity of a product, and nowhere is this risk higher than in the small but essential fasteners that hold components together. Mechanical failures related to fasteners often arise from using standard options that are not suited to the unique demands of the product. This is where custom non-standard fasteners take center stage as a critical solution. By offering exact fits and tailored specifications, they reduce the chances of mechanical failure caused by improper fastening. Vodafast, a leading fastener manufacturer, goes the extra mile to create high-quality non-standard fasteners that exceed ISO 9001:2015 quality certifications. These fasteners undergo rigorous testing to ensure they meet or exceed industrial strength and safety requirements. Additionally, their diverse surface finish options provide resistance to chemical wear, moisture, and temperature fluctuations, helping to maintain the product’s functionality in extreme industrial conditions. Such durability and performance safeguarded by custom non-standard fasteners make them indispensable for industries facing high-stake engineering demands.
The value of custom fasteners lies in their ability to outperform standard options in terms of durability, safety, and overall product performance. Their precision engineering and material adaptability make them essential for ensuring the structural integrity of complex, high-performing products. Fastener manufacturers like Vodafast are setting a benchmark in the industry, offering tailored fastener solutions that meet the rigorous demands of automotive, construction, and machinery sectors. If you're looking to optimize your manufacturing processes, adopting customized fasteners isn't just a choice—it’s a necessity.
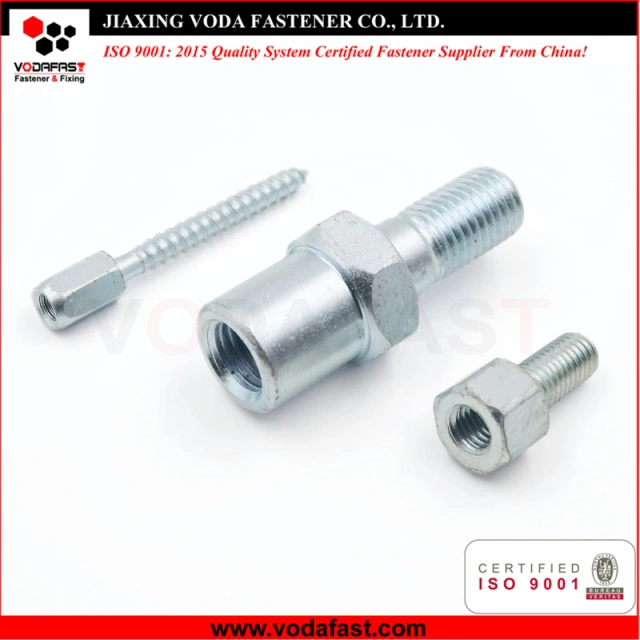
No comments:
Post a Comment