Table of contents:
Key Features of Bearings Designed for Robotic Applications
The Role of High-Precision Bearings in Enhancing Robot Performance
Comparing Different Types of Bearings Used in Robot Reducers
How Specialized Bearings Contribute to the Longevity of Robotic Systems
Key Features of Bearings Designed for Robotic Applications
Special bearings for robot reducers are engineered to meet high performance standards. They are characterized by high precision, exceptional rigidity, lightweight construction, and long life. These features make them ideal for a variety of robot applications, especially in humanoid robots and robot dogs (quadruped robots). These bearings are used in crucial motion parts such as joints, waists, arms, legs, hips, and knees. Their ability to withstand high-frequency shocks and handle complex multidirectional loads ensures the robot's stability and fluidity of motion. Bearings like cross roller bearings, RV reducer bearings, harmonic reducer bearings, and four-point contact bearings deliver unprecedented accuracy, enabling robots to perform with unparalleled efficiency.
The Role of High-Precision Bearings in Enhancing Robot Performance
High-precision bearings underpin the seamless performance of robotic systems by providing smooth and stable movement. For example, bearings used in harmonic reducers such as cross roller bearings and flexible bearings are vital for absorbing axial, radial, and overturning loads, which are common in robotic operations. These bearings also ensure minimal vibration, high-speed ratio, and low inertia, optimizing the balance and stability of robots even under high-frequency motions. Additionally, with their ability to offer consistent rotational accuracy and torque, these bearings contribute significantly to the precision and reliability of robotic actions, vital for tasks demanding accuracy and consistent performance.
Comparing Different Types of Bearings Used in Robot Reducers
Robot reducers primarily rely on harmonic reducers and RV reducers, each with distinct bearing types suited for specific needs. Cross roller bearings, commonly used in harmonic reducers, are available in CSG, CSD, SHG(SHF), and SHD configurations. Their designs range from split outer rings to integral constructions, offering a broad scope to meet specific reducer requirements. On the other hand, flexible bearings, such as HYR, are integral to the compact and efficient operation of harmonic reducers. For RV reducers, angular contact ball bearings provide high rigidity and exceptional load capacity. Each bearing type is meticulously crafted for its intended application, ensuring optimal performance and durability in robotic systems.
How Specialized Bearings Contribute to the Longevity of Robotic Systems
The long-term dependability of robotic systems is heavily influenced by the quality of the bearings used. Special bearings for robot reducers are designed not only for precision and performance but also for longevity. These bearings are built to endure high frequencies of usage and to resist wear and tear over time, thanks to their lightweight yet robust construction. Their ability to withstand complex loads without compromising motion precision ensures that robots operate reliably across extended periods. Using premium bearings provided by trusted bearing supplier or ball bearing manufacturers can significantly reduce maintenance downtime and improve the overall lifecycle of robotic systems.
In conclusion, selecting the right bearings is a critical aspect of ensuring the optimal performance and longevity of robotic systems. High-quality bearings not only enhance precision and reliability but also minimize the risks of unexpected failures, leading to lower maintenance costs and improved efficiency. By partnering with reputable manufacturers and suppliers, businesses can ensure their robotic applications remain durable and effective, securing long-term success in their operations.
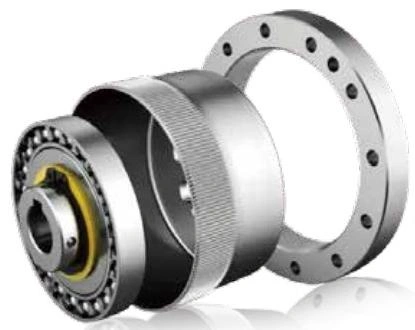
No comments:
Post a Comment